The need for affordable housing in the U.S. has led to new solutions. The 3D printed house is a key innovation. It offers homes that are not only affordable but also sustainable.
These homes are made quickly and at a lower cost. For example, the Grange Close project built three homes in just 12 days. This is 35% faster than usual.
This technology is a big help for cities like Columbus. Home prices there went up by nearly 40% in 2023. The 3D printed house is changing the construction industry in big ways.

Key Takeaways
- The 3D printed house represents a significant step towards affordable housing.
- Construction time for 3D printed homes can be reduced by 35% compared to traditional methods.
- Advanced construction technology allows homes to be built at a lower cost, under $160 per square foot.
- 3D printed homes can be designed to withstand natural disasters, enhance safety.
- Efforts to streamline construction will continue, with future projects aiming for even faster build times.
Introduction to 3D Printed Houses
The housing market is changing fast thanks to 3D printed houses. This new method is a big step in introduction to construction technology. It helps make homes cheaper and more eco-friendly. These houses are built much faster and cheaper than old ways.
Building a 3D printed house can take just hours to days, depending on the design. They use materials like concrete to create the structure layer by layer. This makes it possible to have unique shapes and designs that are hard to achieve with traditional building.
Construction-grade 3D printers cost between $250,000 to over $1 million. This makes building homes much cheaper. Traditional homes in the U.S. cost $100 to $200 per square foot. But, 3D printed homes can cost as little as $10 to $50 per square foot. This big cost savings, along with faster building times, shows the promise of sustainable building solutions.
When printing a house, it’s important to choose the right materials and consider the weather. After the walls are printed, keeping the concrete moist for 24 hours helps prevent cracks. This makes the house strong and durable. The 3D printed house is a big step towards better, more efficient, and sustainable homes.
The Growing Need for Affordable Housing
The housing market in urban areas is facing big challenges. The demand for housing is much higher than the supply. About 50% of Americans say finding affordable housing is a big worry in their neighborhoods.
This issue affects not just individuals but also working-class families. They struggle to find stable homes in the United States.
Homelessness is on the rise, making the need for affordable housing even more urgent. There’s a shortage of 10 million affordable homes. This makes life harder for those in need.
Projects like BioHome3D are trying new ways to solve this problem. They use sustainable materials to build homes that are good for the environment and save energy. They also help reduce carbon dioxide in the air.
The University of Maine’s Advanced Structures and Composites Center is working on new solutions. They use advanced technology to help urban development. This is important because by 2030, three billion people will need better homes.
Traditional building methods are not working anymore. They cause 27% of global greenhouse gas emissions. This makes finding new ways to build homes even more urgent.
Companies like ICON are showing promising results. They can build homes in just eight days using 3D printing. This could be a quick fix to the housing shortage.
These new technologies and materials offer hope. They could help solve the homelessness crisis in urban areas. Advanced manufacturing and eco-friendly materials might be the answer we need.
What is a 3D Printed House?
A 3D printed house is a new way to build homes. It uses additive manufacturing to create structures layer by layer. Big 3D printers make homes from materials like cement mixtures.
This method makes building homes fast and cheap. It’s changing how we build houses, helping solve global housing problems.
Understanding Additive Manufacturing in Construction
Additive manufacturing is different from old ways of building. It builds objects by adding layers, not by cutting away. This tech lets builders make detailed designs and customize homes easily.
The first 3D concrete printed building was made in 1939. The first 3D printed house in Europe was built in Russia in 2017. It was 298.5 square meters big.
How 3D Printing Works in Home Construction
The 3D printing process uses special machines to build walls and structures. It follows digital models exactly. This tech has been used in big projects, like a 3D printed office in Dubai.
Robotic systems, like ARCS, are now helping with 3D printing. They can handle projects from small to very large. This shows how 3D printed homes could be the future.
Advantages of 3D Printed Houses
3D printed houses offer many benefits. They are cost-effective and can be built quickly. These homes use eco-friendly materials and follow green building practices.
Cost-Effectiveness and Speed of Construction
3D printed homes are cheaper to build. Traditional building methods are expensive and take a long time. But, 3D printing can build a house in days or weeks.
For example, 3D printing can build a house in 1.5 months. This is much faster than the usual six months. Automation also lowers labor costs, needing only two to three people to operate a 3D printer.
3D printing reduces construction errors. This is because the building process is precise. It makes homes of better quality and saves money on repairs.
This makes owning a home more affordable. It’s great for areas with a big housing shortage.
Eco-Friendly Construction Practices
3D printing uses eco-friendly materials. It reduces waste, unlike traditional building methods. It also uses advanced materials to cut down on waste.
These homes are well-insulated. This means they use less energy for heating and cooling. Homeowners save money on their utility bills.
3D printing also uses recycled materials. This lowers the carbon footprint of building projects. It supports environmental goals and encourages sustainable living.
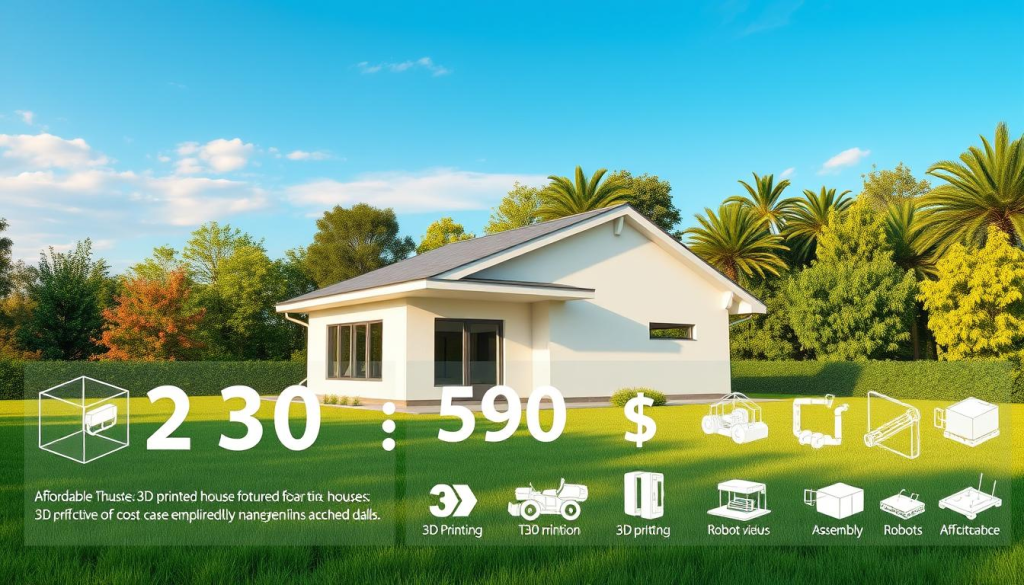
Innovations in Construction Technology
The construction industry is changing fast thanks to new tech and ideas. Automation is making old ways of building seem outdated. It cuts costs, boosts efficiency, and makes things more precise.
The Role of Automation in Building
Automation makes building faster and cheaper. 3D printing is a big part of this change. It lets builders make parts and even whole buildings quickly.
This means projects that used to take a long time can now be done much quicker. It helps meet the need for more homes in a smart way.
Advanced Materials Used in 3D Printing
New materials are key to making construction more sustainable. These materials make buildings last longer and use less energy. They also cut down on waste, which is good for the planet.
As the industry gets more efficient, knowing about automation and new materials is important. With 3D printing growing fast, the future looks exciting and full of change.
Projects Highlighting 3D Printed Houses
The construction sector is changing with 3D printed housing projects. These projects show how construction tech works in real life. Icon is leading the way with its 3D printed homes, making a big impact on the housing market.
Icon’s Impact on the Housing Market
Icon is changing affordable housing with its innovative projects. House Zero, built with Icon’s Vulcan system, won two Architizer A+ Awards and a Texas Society of Architects TxA Design Award. It was also named TIME’s Best Invention of 2022.
Icon’s Project Milestone includes five 3D printed concrete homes. The first home was finished and lived in by 2021. The homes were printed off-site, making assembly quick and saving on labor costs.
Case Studies of 3D Printed Communities
Many case studies show 3D printed homes are effective. For example, a 3D printed house in Riverhead, New York, costs 50% less than similar homes. The PRVOK floating house can be printed in 48 hours and lasts for a century.
In Europe, a two-story 3D printed house in Germany was finished in July 2023. It was made from recycled materials. These examples show 3D printed homes can be fast, affordable, and sustainable.
In Newport News, Virginia, homes cost between $180,000 to $190,000. This is much less than the average price of traditional homes. Texas is also seeing 3D printed homes, like the Wolf Ranch project, which plans to build 100 homes. These homes are priced to compete with the local market.
Project | Location | Details | Completion Time | Cost |
---|---|---|---|---|
House Zero | Texas | Recognized as TIME’s Best Invention | – | – |
Project Milestone | Texas | Five homes, first occupied in 2021 | – | – |
3D Printed House | Riverhead, NY | 50% less cost than similar homes | – | $180,000 – $190,000 |
PRVOK Floating House | – | Designed to last a century | 48 hours | – |
Two-Story House | Germany | Largest in Europe, made of recycled materials | 120 hours | – |
The Future of Housing: A Sustainable Vision
3D printing technology is changing the housing game. As cities grow, this method offers a sustainable solution. It makes homes more affordable and efficient, helping to solve housing shortages worldwide.
Impact on Urban Development
3D-printed homes are changing how cities are built. Places like Austin, Texas, are leading with the world’s largest 3D-printed neighborhood. This aims to ease housing shortages.
Urban planners see 3D printing as a way to build faster and greener. It cuts down construction time and reduces environmental harm. This supports a sustainable vision for cities.
Potential for Global Housing Solutions
3D printing is a global answer to housing needs. Maine, for example, needs 80,000 new homes by 2030. Dubai plans to use 3D printing for 25% of new buildings by 2030.
Projects like BioHome3D show 3D printing’s power to build homes fast and cheap. It’s a game-changer for solving global housing issues. It even helps create homes for the homeless.
Challenges Facing 3D Printed Houses
The path to making 3D printed housing common is full of hurdles. We must tackle tough rules and win over the public. Knowing these obstacles is key to making 3D printed homes more popular.
Legislative and Regulatory Hurdles
Building with 3D printing meets different rules in each place. Codes, permits, and checks can cause delays and extra costs. For example, Alquist 3D’s Muscatine project was delayed a year because of local rules.
As places start to get used to these new ways of building, it’s important to make rules easier. This will help the industry grow.
Public Perception and Acceptance
People are slow to accept 3D printed homes. They worry about how long they last. In Colorado, over 200 people want homes, but getting them to trust these new buildings is hard.
We need to show the benefits of 3D printed homes clearly. We also need to build trust by being open and proving these homes are strong. Stories like Alquist’s can help change minds.
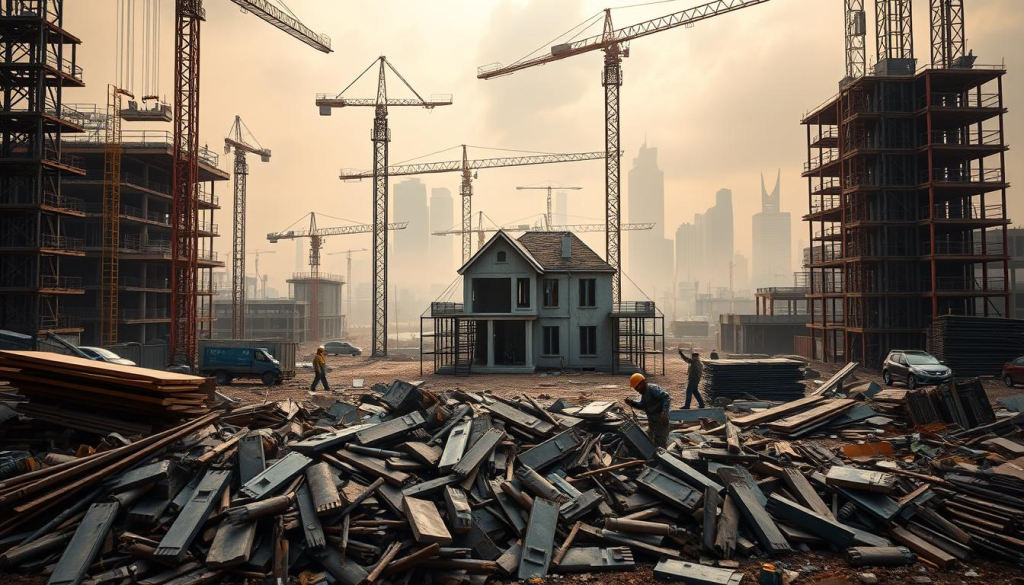
Conclusion
3D printed houses are a game-changer for affordable housing. They can be built for just $4,000 to $10,000, much cheaper than traditional houses. This technology also builds houses much faster, making it a big help in the housing crisis.
Projects like ICON’s work in Austin and 14Trees’ in Kenya show how 3D printing can change neighborhoods. It can bring new homes to areas that need them most.
3D printed houses are also good for the environment. They use sustainable materials and make less waste. This makes them a step towards greener building.
As cities grow, using new tech like robotics in building is key. It makes construction faster and more efficient. Everyone in the housing world needs to get on board with these changes.
For the future, we need to make people understand and accept 3D printed houses. We also need to fix laws that block this technology. And we should keep researching to use more materials in 3D printing.
By using 3D printed houses, we can make living better for everyone. We can create homes that are not just affordable but also sustainable and welcoming to all.
FAQ
What is a 3D printed house?
A 3D printed house is built using a new method. It layers materials, like cement mixtures, to form a home. This method is faster and more customizable than old ways of building.
How does 3D printing contribute to affordable housing?
3D printing makes homes cheaper and faster to build. Some homes are ready in just 24 hours. This helps solve the problem of not enough affordable housing in cities.
What are the environmental benefits of 3D printed houses?
3D printed houses are good for the planet. They use green materials and make less waste than traditional houses. This helps reduce harm to the environment.
What innovations are paving the way for 3D printed construction?
New tech is making 3D printing better. It uses automation and new materials. This makes building faster and more sustainable, changing the industry.
Are there any notable projects that showcase 3D printed houses?
Yes, companies like ICON have big projects. They show how 3D printed homes can change the market. These projects also show new ways to design homes in cities.
What does the future hold for 3D printed housing?
3D printing could change how we build homes. It offers solutions to global housing problems. As cities face housing shortages, this tech could make homes more accessible and green.
What challenges do 3D printed houses face?
3D printed houses have some big hurdles. There are laws and rules to follow, and people might not understand new tech. Getting past these issues is key to making homes more affordable.